TWISTED TUBE®
Heat Exchanger Technology
The innovative design of our TWISTED TUBE® Heat Exchangers delivers more efficient and more reliable performance than conventional shell and tube heat exchangers. TWISTED TUBE® Heat Exchanger Technology features a revolutionary bundle construction that increases heat transfer and reduces pressure drops—while increasing heat transfer surface area and eliminating damaging vibration.
Additionally, dead spots are eliminated where fouling can accumulate and reduce effective heat transfer surface area. See what a difference TWISTED TUBE® Heat Exchanger Technology can make in your operations.
CONTACT US
Call us today to speak with one of our heat transfer specialists: (+1) 713.466.3535 or click to contact us below:
After-Hours Parts Support
inquiry@metalformsht.com
Plug-and-Play Solutions
The TWISTED TUBE® Bundle is designed as an easy retrofit solution for your existing shell and tube layout. No additional piping changes are necessary. It’s as simple as taking your old less efficient tube bundle and replacing it with a better solution. The difference is that TWISTED TUBE® Heat Exchangers can be more efficient and reliable.
Our innovative design eliminates baffles and damaging tube vibration. The uniquely shaped tubes are arranged on a triangular pattern that provide adjacent support as fluid swirls freely alongside. Gaps between the tubes make it easier to clean on the shell side. Rounded ends allow for the use of conventional tube-to-tubesheet joints.
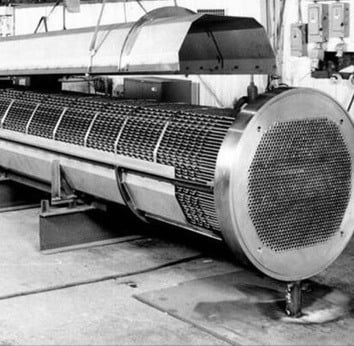
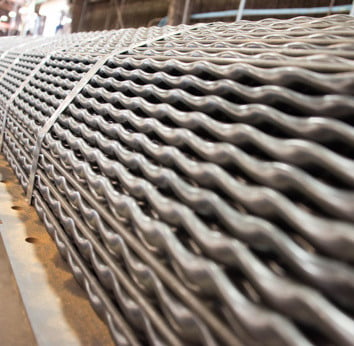
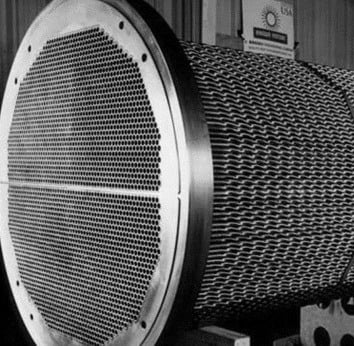
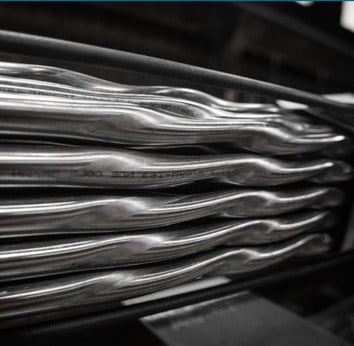
Benefits
Elimination of Damage-Induced Vibration
Due to the generally longitudinal flow pattern of the shell-side fluid and the multi-point support structure of the bundle, the potential for flow-induced damaging vibration is mitigated.
Increased Heat Transfer
Allowing for more surface area in a given shell size, the throughput can potentially be increased based on the application. Increasing the tube-side heat transfer coefficient can provide increased heat transfer, based on the application.
Reduced Pressure Drops
The longitudinal flow allows for a lower relative pressure drop when compared to segmental baffle designs.
Potential Fouling Mitigation
The elimination of shell-side baffles eliminates dead spots where sediment can accumulate and cover heat transfer surface area.
The swirl flow on the tube side increases the shear velocity, ultimately decreasing the fluid boundary layer.
Reduced NOx and Emissions
TWISTED TUBE® Heat Exchanger tube bundles can enhance performance and increase the outlet temperatures of your crude oil or feed upstream of a fired heater, reducing energy consumption and NOx emissions from those fired heaters.
Common Applications
- Crude preheat
- Feed/effluent for:
- Reformer (CCR and semi-regeneration)
- Hydrotreater
- Hydrocracker
- Alkylation
- Overhead condensers
- Reboilers (kettle and J-Shell)
- Lean/rich amine
- Compressor interstage coolers
- Texas Towers
- Hydrotreating/Reforming
- KBR Rose Exchangers
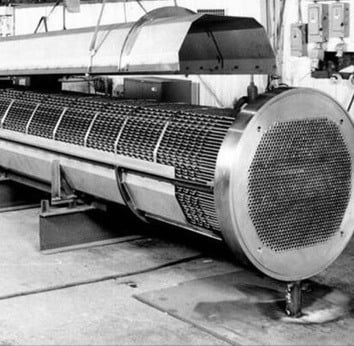
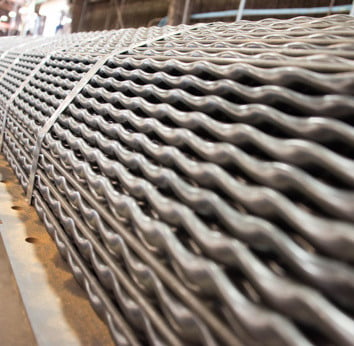
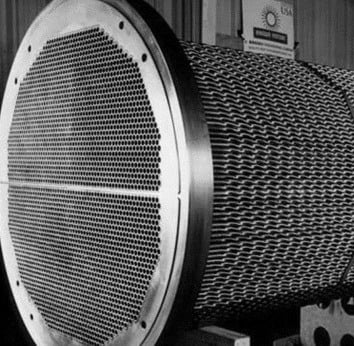
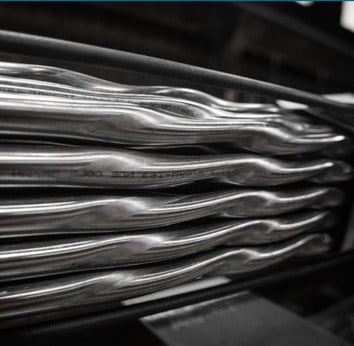
Features
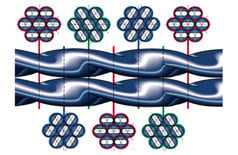
Baffle-free Design
The tube geometry allows for the tubes to be self-supporting, eliminating the need for baffles.
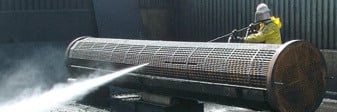
Cleanable Triangular Pitch
The assembly geometry creates multiple cleaning lanes, which allows for the center of the bundle to be accessed.
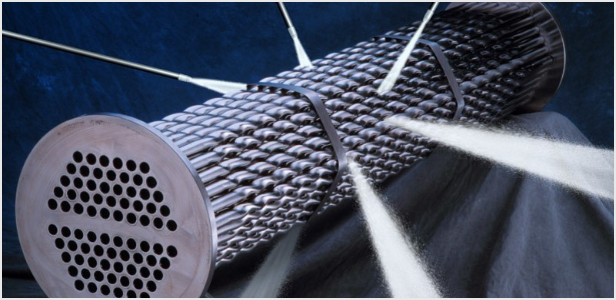
Compact Tube Bundle
Due to the self-supporting tube geometry triangular pitch, more tubes can fit into a single shell size as compared to conventional round tubes.
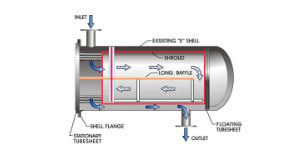
E-F Conversion
The shroud design of the TWISTED TUBE® heat exchanger allows for a more efficient F bundle used inside an existing E shell. The shroud creates a two-pass configuration and eliminates a full-length leaf seal that would be prone to damage.